Introduction to Fall Protection
Fall protection in manufacturing plants is an often overlooked safety measure.
Last year there were over five thousand OSHA violations for fall protection.
Each one of those violations means fines for the business which didn’t implement proper fall protection equipment and procedures.
Falls are also one of the leading causes of workplace injuries and fatalities.
Taking simple steps could prevent many of these injuries and deaths, and most of these OSHA violation fines.
Mistake #1: Improper Protection at Certain Heights
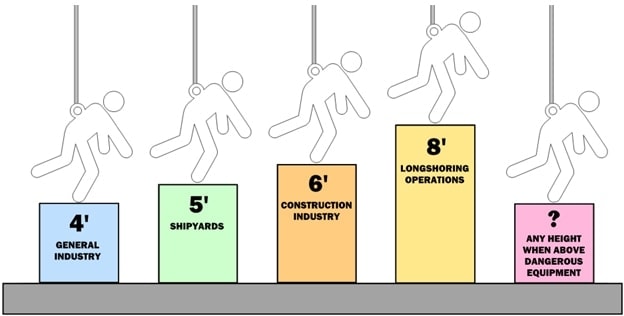
The first mistake you might be making with your fall protection is not knowing how to properly set your fall protection.
This will vary depending on which industry you’re in.
For general industry fall protection must be provided for elevations at 4 feet and above.
That requirement increases to 5 feet for shipyards, 6 feet for the construction industry, and 8 feet for long-shoring operations.
Those are some of the standard requirements for different industries.
We also need to keep in mind how much slack certain kinds of fall protection is allowed to have.
In cases where a worker needs to wear a fall protection harness, they should be aware of exactly how much slack to put in their lanyard.
OSHA requires no more than 6 feet of free fall allowed by your fall protection system.
This does not mean that you should give everyone 6 feet of slack!
Some situations require less than 6 feet of slack.
You will need to adjust your fall protection slack to your specific situation.
Always make sure you don’t have more slack than the distance between your worker and the ground.
Also for factories it is crucial to know what equipment your employees will be working around or over.
You need to make it just as difficult to fall into a dangerous machine as it should be to fall to the ground.
Mistake #2: No Protective Barriers on Raised Surfaces
The next worst thing to not having proper fall protection at different heights, is having no fall protection at all!
You need to make sure that any walking area or work area that is elevated 6 feet off the ground has protective barriers on its sides.
I wouldn’t want to be on a high platform without any rail there, and neither would any of your employees.
If the raised area is a walking surface there will be a rail height requirement of at least 39 inches.
That measurement is the distance above the walking surface.
Because 39 inches is the absolute minimum allowable distance, I would recommend that you go with something greater than that.
The standard seems to be 42 inches.
You can also have rails whose height exceeds 45 inches provided they meet all other fall protection criteria.
While something like guardrail height might seem arbitrary, it is crucial to keeping a safe work environment and avoiding any fines from OSHA.
Mistake #3: Using Body Belts
The third mistake with fall protection which is common in manufacturing is using body belts instead of a full protective harness.
Body belts are a great piece of equipment, but they are for positional safety not fall protection.
This means that they are used to prevent workers from getting too close to the edge of some platform.
They are not meant to keep that worker suspended in air, should they fall off the platform.
The way the body belt is designed makes the impact from a fall centrally located to a person’s waist or lower back.
This can cause serious injury and be very dangerous if the person is stuck in that suspended position for a long period of time.
A full fall harness on the other hand will spread the force of a fall around more of a person’s body.
This keeps the impact of the fall from being centralized, and allows a person to be suspended in the air safely for longer periods of time.
So if there is a risk of someone falling, fall harnesses may be required.
There are no minimum height requirements for fall protection systems, so to learn more about when you should implement full fall protection harnesses you should consult OSHA’s requirements.
Mistake #4: Unsafe Scaffolding
Scaffolding is a great piece of equipment, and provides workers with an adjustable and sometimes movable platform to work on.
Scaffolding can also be built very high.
Because scaffolding is so widely used and can reach great heights, there are a lot of rules that must be followed when using scaffolding.
One rule is that each employee working 10 feet above the next lower platform must be protected from falling to that platform.
This applies whether you’re 10 feet above the ground or 100 feet above the ground.
You cannot allow an employee to fall 10 feet from the platform they are on.
That is just one OSHA rule for scaffolding, to read more about OSHA’s rules click here.
Mistake #5: Using Fall Protection Systems for Other Purposes
Fall protection is vital in keeping your workplace safe.
Because it is so vital, you need to make sure it is treated well and only used for its intended purpose.
Using fall protection to hoist equipment or materials can damage it and cause it to fail when it is needed most.
Using fall protection lanyards as you would use regular rope or straps will cause it to wear out quickly and will make it unsafe to use as it was intended.
Any fall protection equipment that is not fixed to a surface like railing, needs to be stored in a safe accessible location and not with equipment that might get confused as fall protection.
So keep your harnesses and lanyards away from any straps or body belts.
Likewise there have been many videos online of workers being suspended in air by their fall protection harnesses as a joke.
Using your fall protection equipment like this will lead to it wearing out and can be dangerous to any worker who is goofing off with work equipment.
Mistake #6: Not Making Sure Your Equipment Is Fully Functional
Some of the best rock climbers in the world have died due to equipment failure during a fall.
Most of your employees aren’t world class rock climbers, so it is crucial that you make sure all of your fall protection equipment is fully functional before it is needed.
This means several checks should be done.
Checking attachment points on equipment to make sure there are no weak attachments.
Checking fall lanyards for any cuts or frays which would decrease their capability of supporting a falling person.
Making sure guardrails are still solid and don’t wobble when you push on them is a very important check to make.
Replacing old fall protection equipment is another crucial point.
Ideally you would buy quality fall protection like the lightweight systems sold by PWI so you don’t have to worry about replacements for a long time.
But should you choose to go with other fall protection systems, always keep an eye on how worn out it is getting and how durable it is.
Testing this durability frequently can also be a huge part of keeping your workers safe.
Hoping your fall protection works just in case something happens is much worse than knowing your fall protection will work in case something happens.
Mistake #7: Improper Or No Training For Fall Equipment
You don’t want to train your employees on how to use their equipment right before they need to use it.
It happens time and time again.
On the job training happens right when they’re on the job.
This leads to improper harnessing and workers not knowing when something is wrong with their fall equipment.
Fall protection training should happen with two feet planted firmly on the ground.
Proper fall protection training will ensure your workers know how to use fall protection equipment.
And when it comes to fall protection harnesses, take an extra couple minutes to have your workers put the harness on and take it off a couple of times.
Repetition is key with just about everything and that includes knowing how to properly secure a harness and get it fitting properly.
It may seem fairly straightforward at first, but going over the process again could save someone’s life and that is worth the time.
Review
Worker safety should come above all else, that is our responsibility as business owners.
Knowing the most common mistakes with fall protection is step one of making sure that your employees are operating safely.
Step two is making sure you are implementing all of these changes.
You could have all of these mistakes and solutions memorized, but if you don’t make sure these safety measures are being implemented they will do you no good.
Step three is getting quality fall protection equipment.
Replacing faulty fall protection equipment will add up over time. It is much safer to go with a higher quality product that will last longer and be extremely reliable when you need it to work.
Choosing something that is lightweight and doesn’t get in your employee’s way while they work is just as important as how much a system costs.
It’s even better when you can get a system that is both lightweight and affordable.
Contact PWI for the best factory fall protection equipment available and to learn more about what your business needs are for fall protection systems.