Introduction to Mezzanine Floor Options
If you’ve been in the market for a mezzanine for a while, you’ll know that there are many different options to choose from for each part of the mezzanine.
From the kind of steel which goes into the mezzanine’s construction, to how many stairs it has, mezzanines are completely customizable to your needs.
But this also means there is no “one size fits all” mezzanine out there, prebuilt and ready to buy that is just the right size and cost for you.
You will have to think about each aspect of what you need from your mezzanine before it gets built.
In this article I aim to help you with one important aspect of mezzanines – their flooring options.
Aside from the structural supports and guard rails, a mezzanine floor is one of the most important parts to your mezzanine and will greatly affect the overall cost.
Now before we dive into the differences between our flooring options, we’ve got a couple questions to answer first so we’re all on the same page.
What is mezzanine flooring?
The first question you might have is, “What is mezzanine flooring?”
Mezzanine flooring is, as the name implies, flooring for your mezzanine.
But it is more than just any old floor. It is what you’ll be putting material on, or workstations, or offices.
So weight considerations are very important when it comes to selecting flooring for your mezzanine.
No matter what material you choose, it needs to be strong and supported.
A lot of mezzanine floors will have some kind of material underneath them to act as a subfloor.
Sometimes it can be just metal bars which the floor sits on, other times it can be metal decking. We get our metal decking (B Deck and Form Deck) from Structural Deck. They have next day pick up or 2-day delivery in Indiana, Ohio, Michigan, Illinois, and Wisconsin.
Each material I will discuss in this article I will also talk about the relevant sub-flooring options.
What material is used for mezzanine flooring?
There are three different main kinds of flooring which are used in mezzanines.
We will dive deeper into the specifics of each type of floor, but the three main types of flooring for mezzanines are AdvanTech, ResinDek, and concrete.
How thick is a mezzanine floor?
A mezzanine’s floor can vary in thickness.
Floor thickness is usually a few inches for AdvanTech and ResinDek floors, but concrete floors are usually thicker.
A mezzanine’s deck thickness is different from its floor thickness.
When someone refers to a mezzanine’s deck thickness, they are referring to the measurement between the bottom of the primary framing member and the top of the deck.
Option 1: AdvanTech
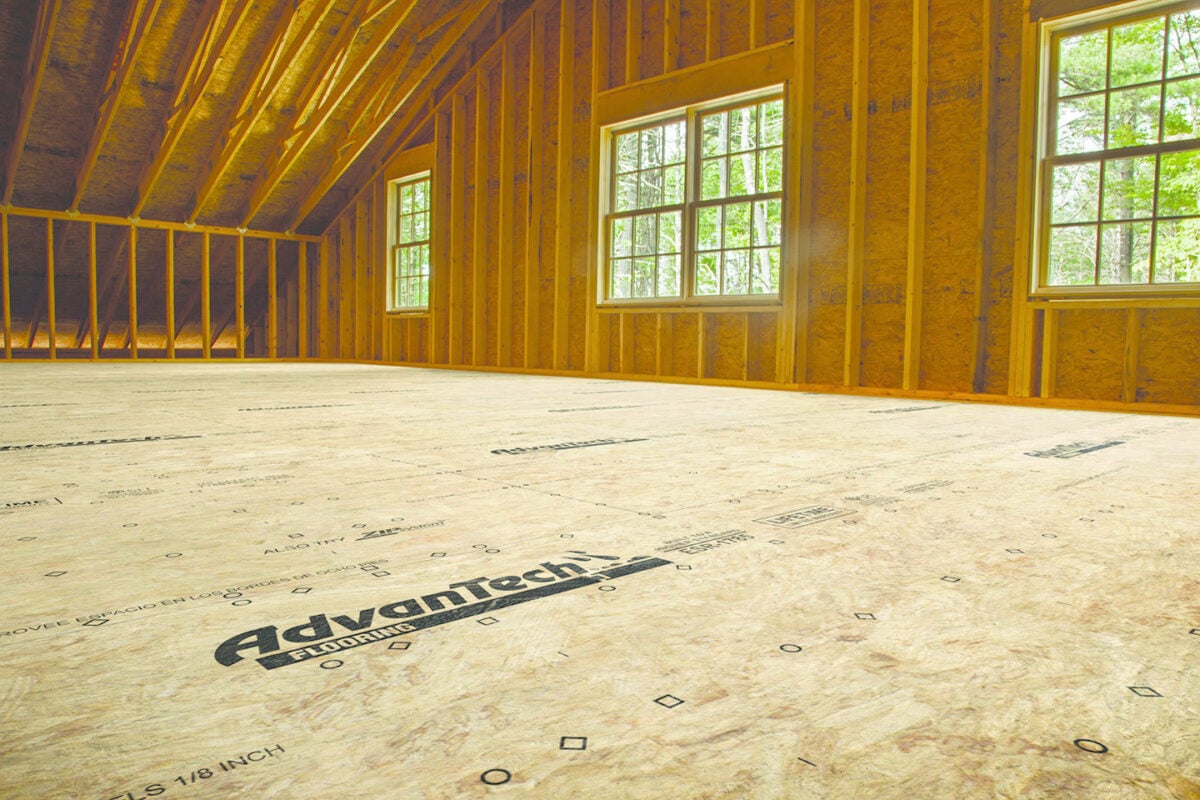
AdvanTech is a type of OSB which has been specially designed to resist moisture and be more structurally sound than typical OSB.
AdvanTech has many advantages over typical OSB, from the higher quality resin they use to the full panel strength tests they use to ensure maximum strength out of their panels.
The AdvanTech panels also have a 500 day guarantee on moisture resistance.
This is very important for building contractors who use AdvanTech to build subfloors in homes, but it is also an important consideration for using it on mezzanines.
If your mezzanine is frequently exposed to moisture, then you would appreciate the benefits of having a moisture resistant floor.
As far as price goes, for AdvanTech flooring at the time of writing this is $73 for a single 4ft x 8ft sheet.
Keep in mind that the total price for flooring will also depend on the kind of supports you use for the floor, but in general Advantech is usually the most affordable option for flooring.
Option 2: ResinDek

ResinDek is a really interesting option for flooring.
A ResinDek floor is a wood panel that has a top layer fused to it.
What is interesting is that depending on your needs, you can customize the top layer of the ResinDek floor.
They can be customized to accommodate anti-static needs, the use of moving robots, and durability against the wear from pallet jacks.
ResinDeks are typically mounted on top of a metal decking system to further ensure structural integrity and prolonged durability.
ResinDeks can also offer an increased shock resistance that isn’t found on concrete.
This is a great benefit if you have lots of foot traffic on your mezzanine as it will reduce the impact on your workers’ joints from walking around or standing a lot during their work hours.
Because ResinDeks are so customizable with the types of top layers they can have and level of options to choose from it can be difficult to generate a fixed price.
A good estimate is that a ResinDek will be around $90 per 4′ x 8′ sheet. This can change depending on if you choose additional options that are non-standard.
Option 3: Concrete
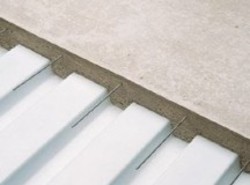
The third option for mezzanine flooring is concrete.
Pretty simple, and easy to understand that if you need to hold a lot of weight your best option is concrete.
The concrete will usually be poured onto a metal decking, similar to the one that ResinDek is mounted to, and will have a steel grating inside to keep it incredibly strong.
Concrete is a great option for a mezzanine floor, but it is not without its drawbacks.
Concrete will be your most expensive mezzanine flooring option. Right now, we estimate that concrete flooring will cost roughly $3.25 per square foot.
So to get the same coverage as a standard sheet of AdvanTech or ResinDek (4′ x 8′), concrete would cost you $104.
It will also be the most expensive option to repair.
If your AdvanTech or ResinDek floor gets damaged you can easily replace a panel of the floor.
If your concrete floor gets damaged you will have to put a lot more work into repairing it.
Comparing All 3 Mezzanine Floor Options
We’ve talked about each option of flooring separately, but it would be helpful to know what are some of the best use cases and their pros and cons.
Use Case 1: You are using a mezzanine to add office space to your building instead of moving to a larger building. The mezzanine will be used to hold office workers and cubicles, but not pallets full of stock.
Use Case 2: You are using a mezzanine to add storage or manufacturing workspaces. It is possible that you will have robots to place and retrieve material from storage. The mezzanine might also have heavy foot traffic from workers.
Use Case 3: You are running out of space in your warehouse and need to store very heavy items for long periods of time. Or you need to place very heavy machinery on the mezzanine. There will be some foot traffic but not robot movers.
Looking at these use-cases, and thinking back to our flooring options we can begin to see that some options make more sense than others.
Use Case 1 Flooring Solution:
For the first use-case it wouldn’t make sense to have a concrete floor.
That would be needlessly expensive, and overkill for the amount of weight it would hold.
It would also be very uncomfortable for your office workers who would have to walk on hard concrete all day.
A better option for the first use-case would be either AdvanTech or ResinDek as they are much easier on people’s feet, and cheaper than concrete.
Personally I think AdvanTech would be the best option for use-case number one.
Use Case 2 Flooring Solution:
For the second use-case I think ResinDek would be the best possible option.
It would provide comfort for heavy foot traffic, plenty of support for storage, and be robot friendly because of ResinDeks’ designed compatibility.
Concrete could be used for the second use-case, but it would come with some problems.
Concrete would be uncomfortable to walk on for long periods of time, and it could throw robots off their path if it were to crack.
If your needs are similar to the second use-case I would go with ResinDek.
Use Case 3 Flooring Solution:
You can probably already tell what option would be the best for use-case number three.
Concrete would be the perfect option for anyone who needs to put some very heavy things on their mezzanine.
It’s even better if foot traffic isn’t much of a concern.
If foot traffic is a concern then you could always put some mats down along workstations or walkways which won’t have pallet jacks running across them.
Concrete is the most expensive option for flooring but for this use-case it would be entirely worth the higher cost.
Wrapping Up
You now understand some of the pros and cons of the mezzanine flooring options as well as their relative costs.
Because mezzanines are so customizable it is very difficult to say “Your floor will cost X amount of dollars”, but you know which option will be your cheapest (AdvanTech) and which one will be the most expensive (Concrete).
It is also important to understand that each of these flooring options heavily rely on commodities, which have been rising in price over the last year.
That rise in price will also affect the total dollar amount you spend on your flooring, but unless something very strange happens the relative price should stay consistent.
Basically, if someone quotes you more for an AdvanTech floor than for a concrete floor I would probably take my business elsewhere.
If you have any questions which haven’t been answered in this article or want to know where to get the best mezzanine floors, contact PWI.
They can help you figure out exactly what will fit your needs and how to get the best available price.
See Also