Why waste money on expensive mezzanine flooring that doesn’t suit your business? Discover how picking the right material can improve productivity, safety, and even noise levels in your facility.
What is mezzanine flooring and why does it matter?
When customers consider adding a mezzanine to their production space, the first question they often ask is, “What’s the best flooring material?” As someone who’s helped many clients navigate this process, I can tell you that choosing the right material is about durability, budget, and even your industry’s specific needs.
Let’s break down the common types, their benefits, and which one might be the best fit for you.
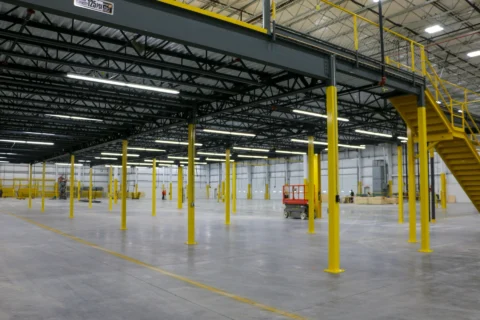
Subfloor vs. finished flooring: what’s the difference?
- Subfloor: This supports your finished floor. Usually made from galvanized steel decking (B-decking or form decking), it’s corrugated and provides structural integrity.
- B-decking: Generally used under composite or wood floors.
- Form decking: Typically used when pouring concrete floors.
- Finished floor: This is the topmost layer people actually walk on. Options vary widely:
- Composite materials (like ResinDek or Advantech)
- Wood/plywood
- Concrete
- Tread plate (diamond plating)
- Bar grating
Some flooring materials don’t require subfloors and can attach directly to structural beams or joists.
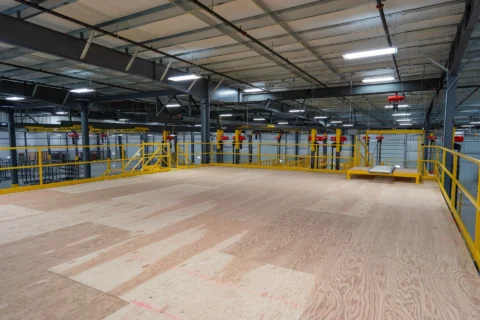
Structuring your mezzanine floor
At PWI, we typically construct mezzanines using either bar joists or structural steel (wide flange beams). For flooring, here are the steps.
- Building the structural base.
- Adding a subfloor (if required).
- Installing your preferred finished flooring.
Compared to some competitors who form flooring structures from steel sheets or plates, we focus primarily on proven methods using bar joist or structural beams for maximum reliability and strength.
Are there codes for flooring material?
OSHA doesn’t specifically mandate flooring types. There are only two main criteria OSHA require:
- Flooring must support required loads.
- It must offer non-slip surfaces that are cleanable and dry.
Beyond these guidelines, selecting materials is entirely application-specific rather than governed by strict codes.
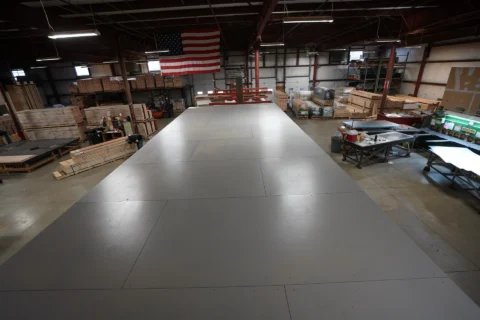
Factors to consider when choosing mezzanine flooring material
To guide customers through their flooring decision, we always examine three critical factors:
- Budget: What’s your priority in terms of initial investment versus long-term durability?
- Intended use: What are you going to use the mezzanine for, heavy equipment, rolling pallets around, or liquid storage?
- New vs. existing facility: New vs existing can change the final cost so it is good to know early on what you are thinking.
Flooring type breakdown: pros and cons
Concrete
Concrete floors offer superb durability, significant noise reduction, and long lifespan. However, installation is more complex and costly; it requires external contractors. Also, concrete makes future mezzanine adjustments more difficult.
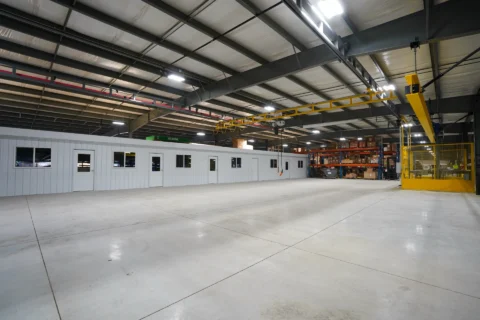
Wood/OSB
This is the budget-friendly, flexible choice and is very popular in industries like RV manufacturing due to changing layouts. However, wood decks aren’t as durable and tend to develop squeaks over time as fasteners loosen.
Composite (like ResinDek)
ResinDek has a coated composite surface, making it durable, resistant to spills, and easy to sweep. It’s significantly pricier than OSB decking—on average $40-$50 more per sheet—but may offer superior longevity.
Tread plate
Diamond-patterned tread plate flooring provides excellent durability under heavy carts or machinery. However, it involves substantial labor costs due to the heavy lifting, welding, and installation steps involved.
Bar grating
Typically used outdoors, bar grating is expensive, heavy, and difficult to install. It’s ideal for applications needing drainage and excellent strength (like outdoor HVAC units) but seldom used indoors due to practical constraints and high cost.
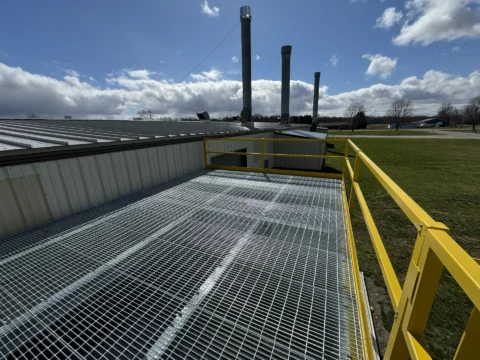
Most popular flooring materials
Based on my experience at PWI, the two most common flooring choices are:
- Concrete (for offices, manufacturing plants seeking long-term durability)
- Wood/OSB (popular in flexible spaces or leased buildings, exceptionally common in RV manufacturing)
What’s the easiest to install?
If you plan a DIY mezzanine—such as for your own shop—the easiest and most cost-effective is wood/OSB decking. On the other hand, concrete installation, tread plates, or bar grating involve specialized skills, equipment, or contractors.
Material strength and durability ranking
If strength and durability are critical, your options stack up like this (from strongest to least durable):
- Concrete (strongest, most durable, quietest)
- Bar grating and tread plate (excellent strength and durability, good resistance)
- Composite materials (ResinDek, etc.)
- Wood/OSB (least durable, susceptible to wear and tear and moisture spill risks)
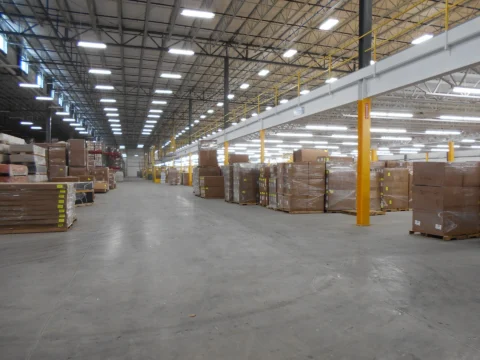
Special mention: stress core flooring
An alternative solution customers often explore is stress core flooring—pre-cast concrete slabs traditionally used by general contractors in new construction. Stress core typically offers greater span distances with fewer supports, reducing floor thickness and maximizing clearance underneath the mezzanine. While we’ve often competed against it, stress core can be an excellent solution if your primary need is long clear-span floors.
In closing
I’ve seen clients choose wood decks for heavy equipment areas, leading to costly and avoidable repairs. Don’t make material choices on price alone—think carefully about your long-term operational needs.
If you’re feeling unsure, don’t hesitate to consult with mezzanine flooring pros who deal with these decisions routinely—like we do at PWI. We’ll guide you honestly, steer you away from pitfalls, and find material options that truly match your needs.
If you are interested in getting a free quote contact us at PWI.